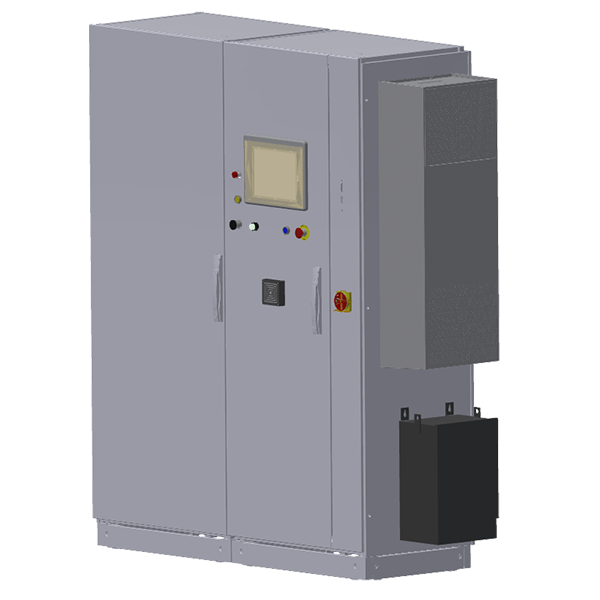
The control system is critical to the proper operation of the pump system. The control system stores all of the operating parameters for each casting job. In some gravity-pour applications, this can amount to many hundreds of “fill profiles.” Each fill profile is stored on an industrial PC and is downloaded to the PLC at the beginning of each job run. Programming of fill parameters is performed by an authorized master operator. But any authorized operator can download fill profiles at any time. Typical fill profiles consist of up to 16 segments of specified time of a specified power. As the profile runs, the pump power is varied according to the programmed fill profile. Since the pump has no moving parts, the only inertia in the system is that of the moving metal itself. This means that the pump delivery pressure can be changed almost instantly to meet the requirements of the casting. Numerous safeguards are standard in the control system to meet safety standards throughout the world. Control systems can also be provided with the capability to report to external systems for such things as SPC and other managerial data systems.
The control panel incorporates controls for automatically compensating for variations in metal level in the holding furnace. This is especially important in gravity casting applications since a very small change in metal level in the launder tube can have a dramatic effect on flow rate. Low-pressure casting is not nearly as sensitive to variations in metal level in the furnace, because the flow rate is not very dependent on how high the metal is in the mold. The control panel also monitors and controls the temperatures in the launder system, and will prohibit operation if the temperature is not within specified limits.
The PG series controls are user-friendly where hands-on command capability is desired. Under rigorous production conditions, a computer or programmable controller can drive the pump. Without operator intervention, complex mold fill parameters, difficult or impossible to execute manually, are easily and uniformly achieved in real-time. To ensure that process commands are accurately met, an optional closed-loop feed-back circuit is available.
The exacting molten metal delivery and tight process control assures maximum casting quality and uniformity, minimal cycle downtime, greatly reduced manpower needs, and fewer scrap castings. The result is significantly improved bottom-line performance.
General Specifications:
- Precision pump controls
- Launder temperature controls
- Pump cooling temperature control