What Is Electromagnetic Pumping?
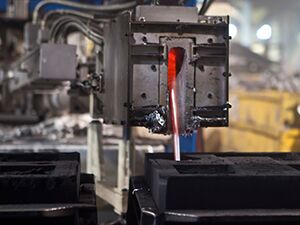
Aluminum and other light metal casting foundries have traditionally used the technique of pouring the molten metal into molds from a ladle, relying on gravity to fill the small spaces in the mold cavity. This must be done very carefully so the molten metal does not experience oxidizing turbulence. The nature of molten aluminum as a strong reactant gives it an affinity to combine with the common components in air, water vapor and oxygen. Humidity in the air can react quickly, creating both aluminum oxide, a ceramic, and hydrogen in solution.
Any oxidized metal that is trapped or forms within the cast part is considered a structural defect and can cause premature failure. The free hydrogen in solution is progressively ejected and forms voids (pinhole porosity) as the metal cools and solidifies, effectively weakening the part. In the past, before aluminum and other light metals and alloys were commonly used, cast parts were large, thick and made of robust iron. Defects caused by the turbulence in traditional ladle pouring were not a big issue.
Today, the market demands greater efficiency in transportation, requiring the use of more parts made of light metals. The advancement of computers has also had an effect. Engineers are designing more refined, structurally accurate parts where minimizing materials investment has a high priority and wasting energy is not permitted. Safety, last but not least, relies on the sound structural integrity of the parts manufactured.
The ideal scenario is for air and water to never touch the melt. Although this is not commercially feasible or obtainable at reasonable cost, the CMI Novacast system is the closest to it, and measures can be taken to further approach the ideal. The amount of melt that is actually exposed to the atmosphere and is introduced into the cast part is at a near ideal minimum.
CMI Novacast builds electromagnetic pumps that draw the molten metal from deep within the furnace where the melt is potentially at its cleanest, then filter the liquid, and pump it up from the bottom or from the side of the mold. Electromagnetic pumps have no moving parts. No metals or contaminants touch the melt. The melt is contacted only by our carefully processed ceramics, so the alloy remains as specified. The launder systems are temperature controlled so the melt stays at the temperature desired. And, since the surface of the “pour” air exposure is minimized, the furnace temperature can be kept lower. Compared with any other pressurized foundry delivery system, the CMI Novacast system has proven to be the lowest cost and easiest to maintain of all. Downtime is reduced to minutes, not hours or days, which allows for more time to fill castings and make profits.