Pressurized Furnace vs. EM Pump
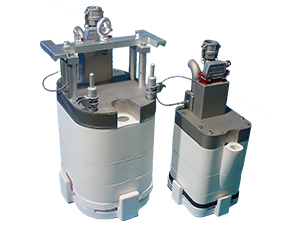
The low pressure casting technique has long been known to produce high quality aluminum castings, but the process has also been plagued by some persistent problems. Many of these problems can be eliminated through the use of an electromagnetic pump as opposed to the standard pressurized furnace.
The pressurized furnace system has several disadvantages which are spelled out here.
- The air above the molten metal bath is pressurized to a high enough level to force the metal up through the stalk and into the mold. Enough over-pressure must be applied (typically up to about 10 psi in the furnace) to feed shrinkage as the casting solidifies. The pressure in the furnace increases the gas pressure in the molten metal also, and when this metal goes into the die, the externally applied gas pressure there is basically reduced to atmospheric, and the gas pressure remaining in the metal causes the evolution of bubbles. These gas bubbles cause porosity and other defects in the finished casting.
- As metal is drawn out of the furnace by the production of castings, the volume of air above the metal increases. This increase can be very large in an operation where the furnace metal level is allowed to drop almost to the point of not having enough metal to produce a casting. It is nearly impossible to control the filling of the casting since the air above the metal is a nearly ideal spring which has continuously changing characteristics as the furnace metal level changes. With a full furnace, the spring is fairly stiff, and as the metal level drops, the spring becomes progressively softer. If varying fill rates during the filling of the mold are required by the casting design, then control becomes almost impossible due to the spring inserted above the metal. Even if the air pressure in the furnace is closely regulated during the filling of the mold, the springiness of the air prevents tight control of the actual metal delivery.
- The furnace is a pressure vessel, which increases the furnace cost considerably. Since this pressure vessel must be opened frequently to add metal, the maintenance of adequate seals around the doors and stalk can become quite a problem.
- When the metal level in the furnace becomes low enough to require the addition of metal, the production of castings must be interrupted long enough for the furnace to be opened, metal added, the skimming of the surface of the bath, the replacement of the sealing materials and closing of the filling door. If the casting weight is high compared to the furnace capacity, this down-time can become a significant percentage of the total machine time.
- During the above mentioned down-time for refilling the furnace, the die temperature is changing, which could result in casting problems and increased scrap rate during the restart period.
- When the furnace is opened to add metal, the actual transfer takes place by bringing a large ladle to the furnace, opening the fill cover and then dumping the metal in. This is a very undesirable method of adding metal to a furnace since it causes much agitation of the bath and produces a great deal of metal oxides in the furnace. These oxides are virtually the same density as the aluminum and hence only the large particles which still have some free air or gas attached to them, rise to the surface where they should be skimmed off. The rest of the oxides remain in suspension where they are likely to be drawn into the casting.
- Leakage past the high temperature seals and the production of castings causes considerable use of compressed air, which is a high cost commodity.
- The press is usually directly above the furnace, and hence, the bottom platen and the lower half of the die are subject to heat distortion problems from the heat coming off of the roof of the furnace.
- To allow for cleaning of the furnace and maintenance of the bath, either the furnace must be able to move out from under the press or the press is required to either tilt over, shuttle away from the furnace on tracks, or lift up away from the furnace. All of these schemes increase complexity and cost of the system. The increased complexity also increases the maintenance cost of the system.
- The pressurized furnace system cannot make use of the ceramic foam filter unless a new filter is placed in the sprue opening for each casting.
Utilization of an electromagnetic pump offers the following advantages:
- Since the furnace is now open, the gas pressure in the molten metal is the same as it is in the die. This reduces the tendency for the gas bubbles to form. Porosity defects are reduced.
- Because the electromagnetic pump doesn’t rely on gas pressure to move the metal, its controlability isn’t affected by changes in the metal level in the furnace. The pump maximum flow rate is affected by the level of metal in the furnace, but in most cases the pump has sufficient capacity to properly fill the mold even when the furnace level is eight inches below maximum.
- There are no seals to maintain since the furnace isn’t pressurized.
- The holding furnace is of conventional design which allows for continuous de-gassing of the metal and also permits metal additions at any time without shutting down the production process..
- Since production isn’t interrupted to fill the furnace, the die temperature remains stable, eliminating restart casting defects and also reducing thermal shock to the die.
- With an open furnace, the transfer of metal should occur more frequently. Doing this means that the thermal shock to the furnace lining is reduced and the metal being added doesn’t free-fall as far. Oxide production from the transfer process is reduced. Also with a suitably designed reverberatory furnace there would be curbs and dams placed to minimize stirring of the bulk of the bath during metal additions and to allow more settling time for impurities.
- There is no compressed air consumption for filling the castings.
- The press in the electromagnetic pump system is normally offset from the furnace by several feet. This greatly reduces the thermal transfer from the furnace to the platen and lower die half.
- Since the press is offset from the furnace, there are no requirements for the press or furnace to move for maintenance. The metal from the pump is conveyed by a closed electrically-heated refractory pipe and is then injected into the bottom opening in the die.
- The electromagnetic pump utilizes a ceramic foam filter against the bottom of the pump where the pump intake is located. In this way all of the metal moving from the furnace to the die is filtered. Metal filtration can significantly reduce casting and machining defects. The life of such a filter is quite long since the filter is continuously immersed and never loses its prime. The cost of such filtration is also quite low since one filter can treat as much as 100,000 pounds of metal before restricting the pump intake too much.
- CMI Novacast also manufactures a device for sensing the actual pressure in the metal delivered by the pump. This device then regulates the applied pump power to maintain the desired pressure in the casting. Since the pump has no moving parts, the speed of response to changing input power is almost instantaneous. This system provides very precise control of the actual metal delivery to the mold regardless of changes in the metal temperature or metal level in the holding furnace.
- Since the furnace is open, one of the new high-efficiency electric holding furnaces could be used which would be fed liquid metal from a remotely located melting furnace by a launder system.
- The launder system is kept continuously full of metal from the melting furnace(s) and all of the holding furnaces are connected to this same launder. With the launder full of metal at all times, the metal level in all of the holders also remains constant. The launder metal delivery system eliminates manpower requirements for metal transfer and allows a long settling time for impurities. The furnace and launder could also be provided with a cover gas of argon or nitrogen to further reduce gas pickup and oxide generation.
- With a launder metal delivery system in place, the reduced gas and oxide pickup also improves the metal loss picture. The flow of metal from the melting furnace to the launder system is non-turbulent and the flow in the launder is very smooth and quiescent.
As you can see from the above, the electromagnetic pump not only provides better controllability and repeatability, but also allows for greater control of porosity and other casting defects caused by molten metal handling and transfer. In addition, the electromagnetic pump allows for simplified and less costly press and furnace construction and provides for greater up-time for the casting station.