Controlled Pouring for Aluminum Castings
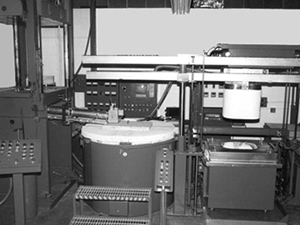
Abstract
The present demand for greatly improved productivity and quality of aluminum castings has brought many developments and continues to force critical evaluation of our manufacturing processes. Handling and pouring of molten metal are two areas where new ideas are being introduced to achieve these goals.
Aluminum is easily damaged when in the liquid state, primarily due to its extremely high chemical reactivity with air, moisture, hydrocarbons, refractories, and other metals. Recovering from the damages is not always easy, so it is better to avoid the conditions that cause them. The effects of such reactions result in (1) metal loss as dross and sludge, (2) degradation of casting soundness and mechanical properties from gas porosity, dross particles and films, (3) altered foundry characteristics, and (4) decreased machinability due to inclusions of various kinds.
Chemical reactions are affected by comparative surface areas and by turbulence. Of these, the latter is a direct function of metal velocity, which also leads to enlargement of surface area. Reactions can be minimized in any flowing metal, such as that in the mold and gating systems, when they are designed to have a coherent liquid mass moving at low velocities. One of the best ways to do this is by injecting metal into the bottom of the mold, rather than pouring in at the top. When done slowly, the metal moves upward in the mold as a body having minimum surface area and no turbulence. Thus gas reactions are minimized, oxides and films are retained only on casting surfaces, cold seams and misruns are not so likely, and internal quality is enhanced. Low pressure casting methods are preferred to achieve these good pouring conditions, and have been successfully applied in several different processes.
For many years pneumatic pressure has been used to force metal out of a furnace or ladling device into the mold, making high quality castings. Recently electromagnetic pumps have been applied as a replacement for air pressurization of the metal. The pump improves control of metal flow rates and has the unique characteristic of responding instantly to commands from the electronic controls. Thus metal entry into mold cavities is fully responsive and follows prescribed recipes governing pump pressure as a function of time. Best quality castings are made when fill-rate is precisely controlled.
Applications of the low pressure casting method are described, and cover its use with chemically bonded sand molds, high production green sand molds, and high pressure squeeze die casting.
Introduction
The recent dramatic market growth for aluminum castings created many new production facilities and also stimulated research and development to improve quality. This is leading to development of better processing methods and improved equipment for making aluminum parts. Our discussion is limited to handling liquid aluminum in the foundry. We will examine some molten metal phenomena and look critically at some of our procedures and metal handling equipment, as they relate to some troubling characteristics of molten aluminum.
Characteristics of Liquid Aluminum
Oxidation Phenomena
The high chemical reactivity of molten aluminum leads to many handling complications related to oxidation and gas reactions. A common means of quantifying this aggressive behavior relative to other oxides is the familiar diagram of free energy of oxide formation as a function of temperature (Figure 1). The diagram illustrates the strong driving force causing aluminum (shown in blue) to take oxygen from all metal oxides above it in the figure. This applies also to gases like carbon monoxide and dioxide (shown in green) and water vapor. These reactions with aluminum form aluminum oxide and that with water vapor also forms free hydrogen.
Figure 1 – Free Energy of Oxide Formation
Gas Absorption
Hydrogen is absorbed through the entire liquid surface, not just its top surface, and easily moves inside because of its very small atomic size. Normally we look only at the top surface of a melt and consider all gas reactions to be occurring there. In fact the permeability of all refractories allows hydrogen to pass through and reach the contained metal, so the entire melt surface area, including that under and around the metal mass, is reacting with gas, especially hydrogen. The rate at which it mixes in a metal mass is very high when the liquid is moving, since it is being carried by the mixing action.
Figure 2 – Metal Velocity Effect on Transverse Strength
Film Formation
Based only on the free energy of formation diagram, it seems that molten aluminum would be converted almost instantly to the oxide. That this does not occur is due mainly to the barrier effect of the gamma aluminum oxide film, which is the first form of aluminum oxide to appear on the aluminum surface. This reaction occurs so quickly that we probably never see un-oxidized aluminum. Instead we see an oxide bag, filled with aluminum. The characteristic of this oxide film has a profound effect on the chemical and fluid behavior of the liquid metal, and ultimately on casting properties. Film growth varies widely depending on alloy content, turbulence, and atmosphere composition. For instance, the presence of magnesium in the melt increases oxidation rates by altering the film composition toward that of a spinel.
Figure 3 – Effect of Transient Gas Passage
Turbulence
Inducing surface turbulence in the melt breaks the film and immediately exposes aluminum to further oxidation (and hydrogen solution). This is true for surface turbulence induced by any means including stirring, bubbling, transporting, pouring, or flowing around obstructions in the mold. Surface turbulence breaks and fragments the thickened films into smaller particles or patches, and frequently the liquid metal movement or surging during pouring causes the entrapment of air or folds these oxide layers onto themselves, leading to air entrapment. Studies by Campbell prove that the film effect is critically related to metal velocity (as shown in Figure 2) by the precipitous drop in transverse strength at a metal velocity of 0.5 meters/second. This is shown for 5 and 10mm plates but was verified in many commercial castings.
Campbell describes how the tangled webs and oxide plates impede flow in channels and molds, reducing fluidity. The crevasses formed by the folds contain gas and are sites for more nucleated porosity and shrinkage cracks.
Trapped oxide films can be formed by entrainment of mold or core gases or passage of such gases through the metal section even after it is in place in the mold (Figure 3). Such film may be continuous through the metal section and have a detrimental effect on casting pressure tightness.
In solid metal the folded oxides are sharp stress raisers, and can drastically lower mechanical properties. They also serve as paths for pressure leaks, and are a plague on machine tool life and machined surface quality. Clearly the potential for defects resulting from turbulence is so great that measures must be taken to avoid conditions leading to surface turbulence.
Turbulence can be beneficial since it improves alloy homogenization and temperature uniformity. It blends additions and enhances contact with fluxes. The desirable goals can be achieved by creating bulk turbulence within the melt body without producing surface turbulence. Deep rabbling or submerged pump circulation are good, and if properly done are not sources for surface turbulence.
Normal Metal Handling Equipment
Having reviewed some aluminum characteristics related to formation of oxides and gas defects, it is now appropriate to examine some of our processes and equipment designs to see how they relate to these problems.
Furnace Selection for Clean Metal
This logic suggests permission to use fossil fuel melting furnaces or induction melters for their operating economies, but to follow them with relatively large electric holders having quiet baths, a long dwell time, and a carefully sealed furnace chamber. This rules out induction furnace use as holders.
Figure 4 – Free-fall Height Effect on Dross Formation
Transporting Molten Metal
Transferring liquid aluminum in the foundry is essential. Even in foundries having a single furnace feeding multiple molds, the metal must be transported to the molds and poured into them. Ordinary techniques using ladle transfer achieve the goal, but damage metal quality.
During metal transfer the temperature drops, surface oxide coatings are disrupted, metal splashes, and oxide is generated. In general the transfer process involves turbulence, generation of films, entrapment of films, and exposure to humid atmospheres. Figure 4 shows one of several mechanisms by which large quantities of air and oxide are introduced during a pouring transfer. The resulting turbulence and air aspiration damage metal properties.
The growing practice of using launder systems, shown schematically in Figure 5, is very important due to the quiescent metal flow obtained. There is very little oxidation. The heated launders are at a constant elevation and have given long service lives of several years without serious failure. Low thermal mass fiber ceramics account for high thermal efficiency.
Figure 5 – Actual Launder System
Pouring the Casting
Gravity pouring is the easiest way to fill a mold, but to keep out dross requires very rapid filling of the sprue, runner and pouring basin. Unfortunately this aspirates a large volume of air. Recent information reports that aspiration takes in an air volume up to 30% of the total volume of metal poured, while using bottom pour ladles entrains a quantity of air equal to the volume of metal poured. Obviously a good pouring device must trap dross, height of free fall must be kept to a minimum, and use of filters in the runner is highly beneficial.
The different automation devices for gravity pouring succeed more or less, depending on their design and use. All pouring devices can achieve good automation, but only a few are able to control metal entry to minimize turbulence, aspiration and gas pick-up. The most common problem is having excess height between pouring device lip and mold pouring basin. Only the metal pumps and pressurized vessels have the ability to reach over a mold while keeping head height to a minimum and controlling flow rate. They also can be equipped with ceramic filters to trap oxides, and inert gas lines to cover the pouring stream.
Low Pressure Pouring
Low-pressure pouring is the preferred method for making quality parts. Metal is introduced from the bottom or side of the mold at low pouring rates so the metal stream does not fragment or diverge, except as dictated by mold shape. Metal moves into the mold as a coherent mass, having minimum surface area for reaction with the environment. Much of the feeding requirement is furnished by metal which is subsequently drained out of the mold, so yields are high.
In the low pressure process metal can be drawn into the mold by vacuum or be pushed in by air pressure, centrifugal force, pressurized furnace discharge, or a pump. Filtering is possible and the filling devices can be fully automated. Most methods draw metal from below the free surface in the furnace at a location where oxide, sludge, and hydrogen contents are at a minimum.
Figure 6 – Defects From Constant Flow Rate
Control of metal filling rate is a desired feature, especially the ability to fill according to a level versus time profile. The reasons are clear from Figure 6, which shows the seams and laps resulting from filling a gravity poured mold at a fixed rate of metal flow, rather than a controllable rate of metal rise. Successful profile filling needs knowledge of the instantaneous metal level in the mold, and then requires the filling device to quickly change the delivery rate so the rate of rise will not stagnate.
Low Pressure Process Using Pneumatic Pressurization
Pneumatic pressure casting is an old method which makes high quality aluminum castings, such as car wheels and engine components. The process had its origin in the U.S. but was exploited most successfully overseas. Pneumatic pressurization of the furnace has for years been the dominant low pressure means of filling the mold, and many improvements in machinery and process control have kept it a viable method still favored by many.
Figure 7 – Pneumatic Low Pressure Casting Machine
Modern units (Figure 7) can use reverberatory furnaces in place of crucibles and thus increase holding capacity and improve furnace life. New ceramic stalk materials are available in lieu of iron, do not contaminate aluminum, and require less maintenance. Addition of PLC controls and solid state devices greatly enhanced operational flexibility so now it is possible to fill the mold under stepped fill-rate pressures, and to allow only a slight drop of metal level in the stalk between cycles. This avoids progressive oxide build-up in the stalk as is encountered when the air pressure is fully exhausted after each cycle. This oxide is likely to be eroded on later fill cycles and be carried into the casting.
Some important operating problems remain which are peculiar to pneumatic pressurization:
- (a) Refilling the furnace always interrupts production, allowing die temperatures to drop, and decreasing overall productivity
- (b) Normally hot metal is brought to the furnace in a large ladle, which inevitably is a rough transfer, and then is poured from some height at a fast rate. This aspirates air, washes sludge from the bottom, and generates much turbulence to make dross and harmful films which do not have time for separation;
- (c) The hydrogen content in the metal is higher as a result of the pressure;
- (d) Refilling is labor intensive and not easily automated;
- (e) Furnace air leaks are a problem;
- (f) Precise control of level and flow rates is difficult due to the springiness of the air column and its changing temperature, and also by the increase of air volume as metal level decreases
- (g) Very fast response is not achieved either since the air system has “inertia” from the large gas volume in the furnace.
From a cost viewpoint, pneumatic pressurized casting equipment is expensive because the furnace must be a pressure vessel. This means that furnace size is limited, the power source usually must be electric, and charging must be a batch operation. Normal maintenance requires separation of the press and furnace, which adds to press cost by adding another motion of the mechanisms and demands a rugged design. Frequently the furnace must be movable as well, sometimes in two dimensions. The requirement for compressed air is a cost factor of consequence, due both to capital cost and air consumption. Compressed air is an expensive utility.
Low Pressure Casting by Electromagnetic Pumping
It was realized soon after development of electromagnetic pumps (Figure 8) that they had important potential for making improved quality parts by applying them to the low pressure casting process. Utilization of an electromagnetic pump offers the following advantages:
Figure 8 – CMI Novacast Electromagnetic Pump
The furnace is open and not pressurized so there are no upper limits on furnace size or type and its cost is minimized. The furnace is not unique, does not need to be part of a package, and any suitable design can be used. There are no sealing problems, and metal in the furnace or well can be accessed for skimming, temperature checks, degassing, and metal additions at any time–without stopping production. Addition of charge material does not have much thermal shock effect on the furnace lining, and the added metal has little or no free-fall, so air aspiration and oxide generation from the transfer process is greatly reduced.
The electromagnetic pump utilizes a ceramic foam filter positioned against the pump bottom where the intakes are located. In this way all metal moving through the pump is filtered. Filter life up to 100,000 pounds throughput can be obtained due to the slight back flush in each cycle.
Figure 9 – Electromagnetic Low Pressure System
The press in the electromagnetic pump system (Figure 9) is normally a fixed position unit and does not need to be part of a package, so again any suitable and simple design can be used. Typically the press is offset from the furnace by several feet. This reduces thermal transfer from the furnace to the platen and lower die half, so they are cooler and cycle time is shorter, resulting in higher production rate. Cooling water or spray can be used safely. Since production is mostly continuous the die temperatures remain very stable and scrap rate is lower.
A pressure sensor connected to electronic closed-loop controls measures and regulates the actual metal pressure in the launder to maintain the desired fill profile and feeding pressure in the casting. Since the pump has no moving parts and metal inertia is slight, the speed of response to changing command is almost instantaneous. This system provides very precise control of the actual metal delivery to the mold regardless of changes in the metal temperature or metal level in the holding furnace. Metal level variations of several inches are acceptable.
In summary, use of electromagnetic pumps in the low pressure system provides better controllability and repeatability, and also reduces porosity, shrinkage, and oxide defects caused by molten metal handling and transfer. In addition the electromagnetic pump allows for simplified and less costly press and furnace construction and provides shorter cycle times and greater up-time for the casting station.
Case Histories
Recent installations can be cited to illustrate some combinations of equipment and devices. The castings made are intended for mass production, are complex in shape, and must meet demanding specifications for high quality. The cases cited are for chemically-bonded sand molds, green sand molds, and squeeze casting dies. But equipment and concepts are applicable to other methods of mold filling and feeding the casting.
Rover Low Pressure Sand System – Production of Blocks and Heads
Rover Group built their LPS (Low Pressure Sand) facility to use chemically bonded silica sand for castings having wall sections down to 3 mm. This plant incorporates the liquid metal handling features discussed earlier. Primary ingot is manually charged to four large electric reverberatory furnaces. The melt furnaces are very well insulated and are carefully sealed to limit air ingress. Heating is by suspended metallic resistance elements. The furnace chambers are partially divided and positive circulation is obtained from pneumatic pumps propelling metal from chamber to chamber in each furnace.
Four melting furnaces discharge to a common heated launder which receives its metal from pneumatic pumps in the melt furnace well. A pair of parallel launders branch from the common header and run between the casting stations to eight holding furnaces. They are joined again beyond the last casting stations to form a continuous supply loop. Every launder section is electrically heated by the reverberatory method and kept at casting temperature. The eight holding furnaces are electric reverberatory units, again very well insulated and kept at a constant temperature. The metal level in the entire launder and holding furnace system is kept constant.
Metal flow in the launders is quiet and there is very little build-up of oxide in the channels, the oxide covering protects against gas pick up and further oxidation. Flow is evidenced only by a slight surface ripple. Gas purging equipment is available at the melting furnaces but is rarely used.
Figure 10 – Low Pressure Sand Casting
An electromagnetic pump (Figure 10) is immersed in each holding furnace well. This elevates the metal through a short vertical launder and into the bottom of a heated tundish directly above the pump. The tundish cover contains multiple discharge ports corresponding to the inlet points in the mold bottom and are coaxial with the risers required by the casting. Metal is kept in the tundish just short of overflow and is held there until the mold is positioned, and then the pump energy is increased to propel metal into the mold according to the established fill profile. Inductive sensors above the mold control filling conditions. After fill the pump power is increased to an over-pressure value to feed volumetric shrinkage developing in the casting, and is held at that power until solidification is complete. Then power is decreased to its normal bias permitting the liquid metal to separate from solid metal and recede into the tundish ports. At that time the mold is removed. Casting yield exceeds 90%. Overall cycle time is approximately 190 seconds. Foundry scrap is below 1%, and the preferred operating mode is 20 shifts per week.
Figure 11 is an overall view of the facility late in the construction stage.
Figure 11 – Rollover LPS System View
Cosworth Low Pressure Fill with Rollover Gravity Feed System
The original Cosworth Process preceded that of Rover LPS and was very similar except it was designed to make castings in zircon sand molds for use in high performance engines and at lower production volume. Both systems are making very good automotive cylinder head and block castings. The LPS system has been in volume production since 1989 and so is very well proven, while the Cosworth method was used for a longer time in their UK plant and on a moderate scale in South Africa for three years and at the Ford Windsor Aluminum Plant for a few years. These installations use a variant (Figure 12) in which the mold is originally filled using low pressure and then immediately is rotated 180 degrees and separated from the pump system, permitting short pump cycles and gaining a higher production rate.
Figure 12 – Cosworth LP/Rollover Configuration
The furnaces used are large cold charge electrical reverberatory melter/holders, sized to permit dross and sludge to separate from the main melt body. The pump is immersed in the furnace well and is supported so it can have some controlled end-wise movement. The pump discharges to a short vertical launder and then into an elbow connected to a slightly inclined horizontal launder. The horizontal launder attaches to a special heated double elbow, which terminates in one half of a swivel joint.
At the casting station the molds are carried by a heavy duty carousel having multiple mold positions. The molds are rigidly clamped into position and can be rotated 180 degrees around a horizontal axis passing through the metal entry port. Metal enters the mold through this single entry port which is located at one end of the mold near the bottom, and is sealed by an expendable swivel-joint of proprietary design.
At startup of the cycle, metal entering the mold fills a large riser cavity and then rises to fill the up-side-down mold. As in the Rover process, the rate of metal rise follows a recipe of pump power increase as a function of time. At completion of filling, the mold is completely inverted by rotating it around the horizontal centerline of the swivel joint, while maintaining tight contact with the launder discharge elbow. After mold inversion the pump power is dropped to the bias level. This is associated with a drain-back of excess metal from the mold into the launder system and pump until a metal level is reached which permits mold separation from the pump/launder system. Some minor spillage is permitted.
When pump power decreases from that required to keep the mold full during inversion, the metal volumetric contraction must be compensated by metal supply from the risers, so it becomes a conventional gravity-fed casting. Separation of the mold permits the carrousel to index to connect the next mold to the launder discharge elbow for start of the next fill cycle. The casting yield is reported to be approaching 70%. The minimum cycle time hoped for is less than one minute, which is the time for carousel indexing, pump connection and disconnection, mold filling, mold rotation and metal drain-back.
Summary of the Characteristics of Each Process and their Advantages
Both processes produce high quality aluminum automotive engine parts in volume production facilities, and appear to be competitive in capital and operating costs. The following comparison does not evaluate differences in melting, transferring, and holding the metal.
Rover’s LPS method captures the advantage of controlled fill rate combined with pressure-fed solidification; use of a larger pump decreases turbulence; molds are handled without causing stress; metal sections can go down to 3 mm; risers are small and easily removed with minimum kerf; yields exceed 90%; finer dendrite arm spacing is found at riser locations; requires more casting stations but at a lower cost per station; and metal handling by launders is excellent.
Cosworth’s LP Fill/Rollover method also captures the advantages of controlled fill rate, but loses pressure feeding during solidification; it uses conventional risers and gravity feeding forces with yields up to 70%; riser cut-off needs heavy duty equipment and has a wider kerf; the top riser is large and cools slowly so dendrite arm spacing is coarse; attains excellent surface finish and dimensional precision due to zircon sand molds; and production cycle for mold filling is short so fewer pouring stations are needed, but each station is more expensive.
Note that the rollover procedure puts the hottest metal in the riser at the mold top favoring directional solidification. Without mold inversion the riser would be at the bottom of the mold and would have the hottest metal. If the casting section size is large, there is a possibility for mass circulation to develop thus carrying the hot metal to the top away from the bottom riser. We know that such mass movement develops rather slowly, and should not be a factor except in very heavy section massive castings. For the automotive parts cited above, mass metal circulation is not important, and certainly would not be so for parts having small metal sections.
High Production of Green Sand Molds by Low Pressure Pumping
Recently Baxi Heating in the U.K. developed methods to bottom fill green sand molds made in DISA vertical parting line machines. The process is identical to normal practices for making these molds, except that the metal is injected into the side of the mold, near the bottom edge, and so it is a low pressure filling technique (Figure 13). The mold is filled slowly with a non-turbulent flow of metal but for a production rate of 240 molds per hour, there is not enough time for the casting to be fed through the solidification interval. Therefore a variety of proprietary shut-off devices have been developed to prevent metal from being discharged from the mold. Internal risers are used to feed metal contraction and solidification shrinkage, so casting yield is only slightly better than it would be for a gravity-poured casting.
Figure 13 – Baxi Green Sand Low Pressure System
The electromagnetic pump is contained in a reverberatory furnace positioned beside the molding line. Metal is pumped up into a short vertical launder, then into an 85 degree elbow, up a heated launder inclined up from the horizontal position by 5 degrees, and then into a heated double elbow connected to the mold side at the inlet. The pump keeps metal in the elbow at a level just short of discharge. When the mold indexes into position the pump power is increased to fill the mold according to the specified profile. A shut-off device is activated at the proper time, pump power drops to the bias level, and the molding line indexes to cast the next mold when it is properly aligned with the discharge elbow.
Permanent Mold Squeeze Casting by Low Pressure Fill
The squeeze casting process uses high pressure vertical die casting machines but the metal is pushed into the mold cavity at a low velocity to avoid splattering and atomization of the incoming metal. This results in high quality parts free of internal gas porosity and shrinkage, and keeps the excellent surface quality of high pressure die castings.
In this process the shot chamber can be filled in different ways, such as pouring by ladle into a fixed position sleeve, pouring into a tilted sleeve which is pivoted into a vertical position, or by injecting the shot into the sleeve from the bottom. When the shot chamber is filled, the piston pushes the metal into the mold, with or without also pressing later at secondary locations to densify critical areas. Shot pressures are on the order of 10 to 20 ksi. At GM Power Train Division there are two large machines, one rated at 700 and another at 1500 tons clamping force, and in each machine the vertical shot chamber is filled through the sleeve side at its bottom corner using an electromagnetic pump.
Figure 14 – Low Pressure Squeeze Cast Fill Process
The pump is located in a large electric reverberatory furnace, which is mounted on rails to index toward or away from the press for ease of launder maintenance (Figure 14). The pumped metal enters into a very short vertical launder, and then into a heated pressure sensor elbow, which connects to a long horizontal heated launder angled upward. The launder connects to a heated S-shaped discharge elbow which is attached to the heated shot sleeve. At startup the metal level is brought up through the launder and into the discharge elbow, and is held there short of pouring. At the time when die closure and lockup is completed, the pump energy is increased to smoothly fill the shot chamber to its required level. After a moment for stabilization of metal level, the piston moves upward slowly and closes the entry port in the sleeve at which time the pump power immediately drops back to bias level. The molten metal retracts from contact with the moving piston, which continues to drive the shot into the mold at programmed velocity. By comparison with die casting the injection rates are very slow and so casting quality is excellent. The process cycle time is on the order of one minute. The parts are suited for use as suspension and structural uses, especially where product liability is a factor.
Summary
The basic principles governing molten aluminum reactions have been reviewed with the objective of using these to make better castings. For production of quality castings it was shown that metal handling absolutely must be non-turbulent and all components of the system must be selected for their ability to make castings free of oxides and porosity. Methods and equipment needed to do this have been described and case histories cited to illustrate uses of low pressure pouring processes. Better quality castings are being made using these methods.
References
- John Campbell, Castings, Butterworth-Heinemann, Ltd.
- Campbell, J. 1988, Material Science Technology
- Sutton, T. L. and Meahe, M. I., Aluminum Castings — A Step Forward into the Next Century, Stepcon 1995.
- Sutton, T. L., A New Technology for Designed and Controlled Filling of High Volume Quality Aluminum Castings, BCIRA International Conference, 1995
- Gouwens, P. R., Production of EPC Aluminum Castings with EM Pumps, AFS Div. 11 Conference, November 29, 1990.
All materials protected by copyright and may not be used without permission of CMI Novacast Inc.